Industries
ARC’s commitment to innovation rests on understanding the unique challenges of metal working markets. Research combined with years of experience working with the end user allow us to provide the most efficient abrasive solutions.
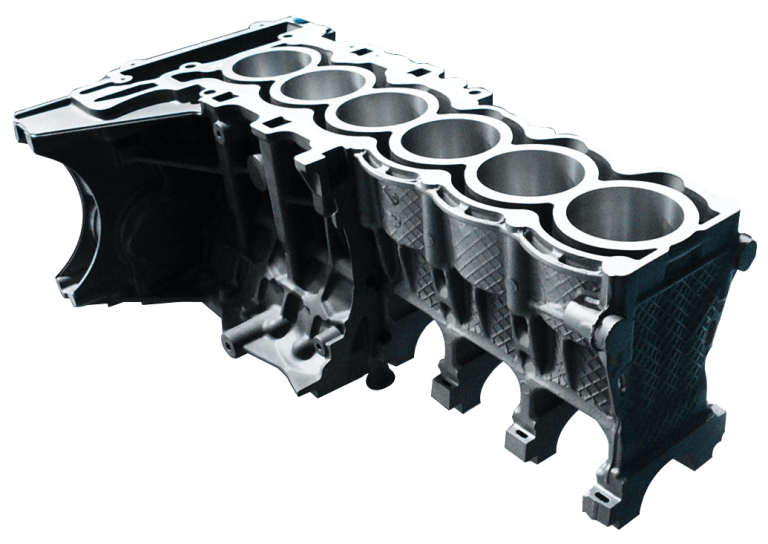
ALUMINUM FABRICATION
Aluminum is one of the most abundant elements on earth. Its excellent properties make it one of the most versatile materials used in manufacturing. Aluminum is lightweight, strong, ductile, joinable, reflective, heat-conducting, electrical conducting, corrosion resistant, non-toxic, non-combustible, and even recyclable. Aluminum is made into three types of flat-rolled products classified by thickness; plate (1/4 inch or more), sheet (between 1/4 inch and .008 inch), and foil (up to .0079 inch). It has hundreds of applications from aerospace and other forms of transportation, to construction and cooking materials.
Aluminum is made into a wide variety of products from airplanes, cars, and spacecraft to computers, bike frames, cans, and foil. Many applications may be involved depending on the final product. Marine and aircraft companies will finish every aluminum part where appearance is crucial. A variety of discs are used, but semi-open PSA discs are recommended. Aluminum fabrication involves a variety of abrasives including cut-off wheels and grinding wheels, flap discs, fiber discs, coated belts, and non-woven products.
Recomended Products
Mild Steel Fabrication
Mild steel is a type of carbon steel also known as “low carbon steel” (up to 0.3%) and essentially contains a combination of iron and carbon. Its low carbon content makes it neither extremely ductile nor brittle. Mild steel is strong, magnetic, and subject to rust if not properly coated. Almost limitless in terms of potential end-products, mild steel’s affordability and ease of use contribute to its use in nearly any project needing vast amounts of metal.
Mild steel fabrication involves making both finished products and components. It is the most common steel around and is everywhere you look. From girders and beams in construction to cars, street signs, pipelines, and fences, mild steel is vastly used. Weld removal, surface prep deburring, and cleaning and finishing processes utilize a wide range of abrasives such as cut-off wheels, grinding wheels, coated belts, flap discs, fiber discs, and non-woven products.
Recomended Products
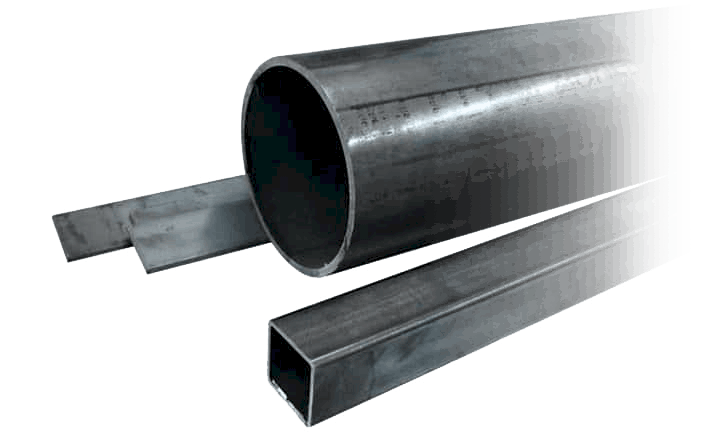

STAINLESS STEEL FABRICATION
Stainless Steel is a steel alloy containing a minimum of 10.5% chromium. Other elements may include iron, nickel, and manganese. Stainless steel is favored for its corrosion resistance, low maintenance, and luster. It does not easily rust, stain, or corrode with water like ordinary steel. Milled into coils, sheets, plates, bars wire, and tubing, its widely used in cookware, cutlery, household hardware, appliances, surgical instruments, and industrial equipment. It is also utilized in the automotive, aerospace, and construction industries. Its corrosion resistance and ability to be sterilized make it suitable for commercial kitchens and food processing plants. There are many different types and grades of stainless steel available and used where the properties of steel and corrosion resistance are necessary.
Stainless steel fabrication is an extremely diverse market with demanding applications. From ID bore polishing to flat finishing a specific Ra value, stainless fabricators follow technical requirements for their applications. The stainless fabrication industry commonly measures scratch depth and relies on the aesthetic finish of products, ranging from tanks and piping to structural components.
Food & beverage and pharmaceutical equipment fabrication are extremely specialized. Intense finishing requirements mandated by the FDA command a specific catalog of abrasive applications. Packaging machinery is similar to food, beverage, and pharmaceutical equipment, due to the similarities in materials used. Industrial valves or fluid transfer valves also require FDA mandates, in which the internal tubing must meet a required finish to pass inspection.
Recomended Products
Brass
Brass is an alloy consisting of copper (70%) and zinc (30%), however small amounts of other metals are sometimes added. Brass is produced by melting copper together with calamine. Nearly 90% of all brass alloys are recycled and reused. Brass has a variety of applications, and its relatively affordable cost combined with its hardness make it valuable for several functions. It is commonly used for musical instruments (such as a trumpet, tuba, trombone, and saxophone), corrosion-resistant screws, and fixtures for baths, doors, and windows. Its resistance to tarnishing makes it optimal for decorative and ornamental objects.
Bronze
Bronze is an alloy typically composed of 60% copper and 40% tin. Its key benefits are hardness, corrosion resistance, and strength. It is stronger and harder than any other common alloy except steel. Tin makes the bronze hard and the strongest bronze alloys contain both tin and small amounts of lead. Bronze has a low melting point and is commonly used for making statues, musical instruments, and bearings. Common bronze alloys expand slightly just before they set, filling in the finest details of a mold. Aluminum is often added to bronze and used in applications where corrosion resistance is desirable such as airplane landing gear, marine engine components, and underwater fastenings.
Copper
Copper is a reddish-colored metal with excellent electrical and thermal conductivity. Copper is malleable and used in a wide variety of products and industries. Copper making requires a four-step process including mining, milling, smelting, and refining. Popular uses for copper include wire, plumbing, household fixtures, statuary, roofing, coins, cookware, flatware, and musical instruments.
Recomended Products